Armé d’une imprimante 3D modifiée, le constructeur de PC Jean Roberto De lacovo a créé toutes les pièces dont il avait besoin pour fabriquer le châssis de ce superbe Boîtier PC imprimé en 3D. Il s’appelle Piñasphere et dispose d’un APU AMD Ryzen 7 à 8 cœurs refroidi par liquide.
Grâce à notre page Facebook de construction de PC en croissance rapide, nous avons vu de nombreux PC de jeu personnalisés, depuis des mods basés sur des conceptions de boîtiers existantes jusqu’à des versions préliminaires. Vous pouvez même soumettre le vôtre pour examen ici même. Pour l’instant, découvrons comment Jean a fabriqué ce superbe boîtier PC imprimé en 3D.
PCGamesN : Qu’est-ce qui vous a inspiré pour construire ce PC ?
Jean : Je voulais voir jusqu’où je pouvais aller avec la conception d’un boîtier d’ordinateur. La norme que les gens imaginent lorsqu’on parle d’un PC est une forme carrée – à quelques exceptions près, la plupart des boîtiers d’ordinateur sont basés sur une forme carrée.
Sur les côtés, vous pouvez voir ces anneaux noirs ondulés – je voulais qu’ils ressemblent aux vagues générées lorsque vous laissez tomber quelque chose dans l’eau. Je jouais déjà avec le motif pomme de pin/ananas pour le dôme à cette époque, j’ai donc pensé que cette idée fonctionnerait très bien également pour les crêtes des vagues, bien qu’avec beaucoup de peaufinage.
L’autre moitié du dôme s’inspire également de la nature : elle est basée sur des nids d’abeilles remplis, et chaque hexagone est complexe quand on le regarde de près. Cette complexité est également utile lorsqu’il s’agit de rendre les lignes de la couche d’impression moins visibles. L’intérieur a plutôt un look de science-fiction avec de nombreux polygones. Sa structure est similaire à celle d’un châssis d’avion : ce n’est pas une sphère, mais une icosphère complexe avec des trous géométriques qui facilitent également la circulation de l’air.
Comment avez-vous planifié et conçu cette construction ?
Habituellement, je commence mon travail avec quelques croquis rapides au crayon et sur papier, mais celui-ci a commencé avec un croquis Tinkercad. Je testais diverses configurations avec des maquettes 3D que j’avais réalisées à partir des composants matériels sur Tinkercad, puis j’ai pensé que si je n’installais pas de GPU et utilisais un bloc d’alimentation externe, je pourrais essayer de créer une forme de sphère divisée.
L’idée première était d’utiliser un cadre métallique fabriqué à la main avec une tôle d’aluminium de 3 mm d’épaisseur. Cependant, j’avais également récemment fait quelques expériences avec l’impression 3D pour fabriquer un appareil photo. Au cours de ces expériences, j’ai testé la résistance du PLA et du PETG et j’ai conclu que le PETG était suffisamment résistant pour supporter les contraintes du boîtier.
Vous avez utilisé l’impression 3D pour l’ensemble de la construction – parlez-nous de votre processus.
Au début, c’était difficile, mais ce serait maintenant un processus beaucoup plus rapide, j’ai dû commencer à le planifier différemment d’un mod de cas habituel, car je ne supprimais pas de matériel mais je l’ajoutais. J’ai fait quelques tests avec différents petits projets afin de pouvoir affiner les paramètres de l’imprimante 3D.
Le logiciel que j’ai utilisé comme slicer pour les impressions était Ultimaker Cura 4.13, je l’ai trouvé intuitif dès le départ et il m’a permis d’affiner mes impressions. Par exemple, j’ai appris à définir l’alignement des coutures en Z pour éviter d’avoir une ligne visible sur les impressions, et à définir les paramètres de rétraction pour différentes situations – vous pouvez essentiellement adapter les paramètres à vos besoins.
Mon imprimante 3D performante est une Creality Ender 3 Pro, que j’ai modifiée car elle était trop bruyante pour moi. J’ai ajouté une carte mère Creality Silent, ainsi qu’un ventilateur de 120 mm pour le bloc d’alimentation, et j’ai également conçu et imprimé les conduits de ventilateur personnalisés pour l’imprimante avec du PETG, ce qui me permet d’utiliser une configuration à double ventilateur Noctua de 60 mm au lieu des ventilateurs standard de 40 mm. .
Il dispose également désormais d’une extrudeuse directe – j’ai dû réduire la rétraction beaucoup plus que prévu, car les premières impressions avec la nouvelle configuration entraînaient des problèmes de colmatage de l’extrudeuse lors de l’impression avec du PETG.
Au total, Piñasphere est composée de 27 pièces imprimées en 3D. Pour la touche finale, j’ai utilisé des couteaux de précision, ainsi qu’un briquet, pour enlever tout excès de matériau ou de cordage. Cependant, une fois que j’ai bien compris les températures du filament, j’ai découvert que le cordage était extrêmement limité.
J’ai également constaté que l’orientation des pièces pendant le processus d’impression aidait en termes de finition. J’ai volontairement choisi la base comme face de contact entre les pièces, car c’est la face avec laquelle on a moins de contrôle sur la finition si on ne la peint pas ensuite.
Un point clé que j’ai appris est que pour obtenir des pièces parfaitement propres avec des couteaux de précision, il faut du temps et de la patience – faites une erreur et vous finirez par jeter la pièce imprimée – c’est ce qui s’est produit avec un cadre SSD que j’ai imprimé. Le nettoyage et la mise à niveau de l’imprimante prennent également un peu de temps, mais ils résolvent la majorité des problèmes pouvant survenir pendant le processus d’impression – l’impression à une vitesse plus lente permet également d’éviter de nombreux problèmes.
Comment toutes les pièces s’assemblent-elles ?
Il s’agit essentiellement d’une structure super-sandwich : comme pour les avions, certaines pièces sont simplement pressées entre les couches fixées. Les pièces sont façonnées de manière à ne pouvoir être assemblées que de la bonne manière – même s’il ne s’agit que d’un coin ou d’un trou différent, chaque pièce a toujours un aspect qui facilite le positionnement. Cette structure m’a permis de créer un châssis suffisamment résistant, mais avec un remplissage minimal, ce qui minimise le poids et la quantité de matériau utilisé.
J’ai ensuite utilisé des vis en inox pour la fixation – la carte mère est fixée à l’aide de vis M3 avec inserts en laiton filetés de 10 mm – vous pouvez les réchauffer avec un fer à souder puis les enfoncer à l’intérieur des pièces imprimées en 3D. Pour le reste des fixations, j’ai fileté le PETG avec des outils et utilisé des vis à tête bombée M5 – les sections filetées font au moins 10 mm de long.
Pendant ce temps, les dômes blancs s’enclenchent simplement du côté de la carte mère et se fixent en tournant légèrement dans le sens des aiguilles d’une montre du côté du radiateur – aucun outil n’est nécessaire ici.
De quelle petite carte mère s’agit-il ?
J’ai utilisé une carte mère ASRock X300M-STX. C’était l’une des plus petites cartes mères que j’ai pu trouver et qui me permettait d’utiliser un AMD Ryzen 7 5700G. Il peut prendre en charge jusqu’à 64 Go de mémoire et dispose de deux emplacements SSD M.2 et de deux ports SATA pour SSD 2,5 pouces, ce qui me laisse suffisamment de place pour mettre à niveau la mémoire et le stockage, ce qui aidera à garder cette machine utile à l’avenir. peut-être comme PC de bureau ou serveur.
Quels défis la forme de la construction présentait-elle ?
Honnêtement, si l’on pense surtout à la forme et non aux dimensions, il est relativement facile de créer un PC avec une forme inhabituelle – le plus grand défi pour moi était de laisser suffisamment de place à l’intérieur du boîtier pour que tout l’équipement fonctionne bien.
Un autre grand défi était les deux panneaux d’E/S : j’avais décidé qu’ils ressembleraient tous les deux au panneau avant, placé dans un renfoncement du dôme, mais je devais également laisser de l’espace pour le cordon d’alimentation. , et c’est pourquoi la « tranche » est si longue de ce côté.
Quel bloc d’alimentation as-tu utilisé ?
Il s’agit de l’alimentation externe fournie avec l’ASRock Deskmini X300. Il ressemble à une alimentation pour ordinateur portable et sa puissance est de 120 W à 19 V – il est plutôt petit, donc il était parfait pour ce PC, car ce n’est pas un monstre gourmand en énergie.
Comment avez-vous planifié le passage des câbles ?
Tous les câbles sont acheminés à l’intérieur de l’anneau central, qui forme également le cadre principal – il comporte de nombreux espaces vides pour la circulation de l’air et l’acheminement des câbles. Les câbles de l’interrupteur d’alimentation, du voyant d’activité du SSD et du voyant d’alimentation sont rangés sous la carte mère, puis placés dans le boîtier qui fait office de crochets pour les dômes et contient également l’interrupteur d’alimentation.
Le câble du ventilateur du radiateur est caché par le crochet du dôme sous le radiateur – j’ai fait un canal d’acheminement pour celui-ci – puis il passe par le passage d’un des tubes de refroidissement et reste caché sous le tube de refroidissement côté carte mère. Les câbles des antennes Wi-Fi sont cachés sous la carte mère et leurs connecteurs sur le dessus de la carte mère sont cachés sous le SSD M.2 afin que vous ne puissiez pas les voir. Enfin, les câbles du waterblock ont été posés sous les « ailes » de fixation du waterblock.
Dites-nous comment fonctionne le système de circulation d’air.
C’est l’une des parties que j’aime le plus dans mes projets. Après avoir traversé le radiateur, l’air passe par le canal central, refroidissant le SSD 2,5 pouces, puis se déplace sous la carte mère et sort par un espace de 5 mm entre la carte mère et son cadre de support – il circule sur presque tout le périmètre.
Mais l’air n’est pas sorti à ce stade : le dôme interne le guide ensuite pour se déplacer autour de la carte mère, refroidissant ainsi les modules M.2 et le dissipateur thermique VRM de la carte mère. Il y a également deux trous sur le côté du radiateur, qui soulagent un peu la contre-pression générée par l’air se déplaçant à l’intérieur du canal central.
Comment avez-vous réalisé les touches cuivrées ?
Je voulais ajouter une couleur chaude pour contraster avec le blanc et j’ai initialement envisagé d’utiliser de véritables anneaux de cuivre. Cependant, pendant la phase d’esquisse, je voulais ajouter plus de facettes réfléchissantes que sur les bagues, je les ai donc imprimées avec une forme plus complexe.
Si j’avais eu beaucoup de temps, j’aurais pu les fabriquer à la main, mais cette fois, je voulais me tester et voir ce que je pouvais faire avec une simple impression 3D, alors j’ai acheté du filament de cuivre de soie Giantarm et les résultats n’ont pas déçu – ils donnent une ambiance premium à la construction.
Quelle spécification avez-vous choisi et pourquoi ?
Je voulais qu’il soit capable de faire un peu de tout, mais l’édition 3D était une fonctionnalité indispensable. Je voulais également que la machine fonctionne correctement dans les jeux en 1080p. Sans place pour une carte graphique, le choix évident était d’opter pour le meilleur APU que je pouvais acheter, à savoir l’AMD Ryzen 7 5700G – je l’adore ; c’est un excellent interprète.
La version dispose de 16 Go de mémoire, car je cherchais le matériel en octobre et novembre, et il était alors en vente. Corsair est une bonne marque, alors j’ai tenté ma chance et je l’ai acheté.
Je mettrai à niveau la RAM dans les prochains mois, car la carte mère ASRock permet d’augmenter la RAM vidéo partagée jusqu’à 16 Go si vous disposez de plus de 32 Go de mémoire système.
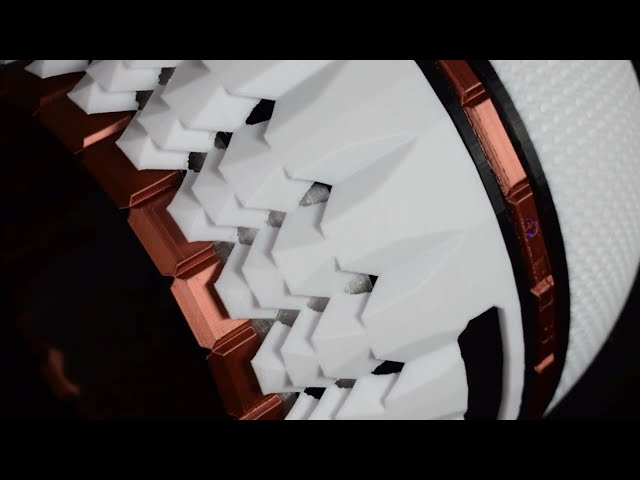
Avez-vous rencontré des difficultés ?
Je pense que le plus grand défi a été d’affiner le profil de l’imprimante pour chaque filament. Je devais réduire les erreurs d’impression impossibles à cacher, car l’un de mes objectifs était de donner une belle apparence à la construction sans avoir à la peindre.
Je me suis habitué au nettoyage en profondeur de l’extrudeuse et j’ai également acheté une longue aiguille en acier inoxydable pour en éliminer tous les résidus de filament.
Combien de temps vous a-t-il fallu pour terminer cette construction, du début à la fin ?
Après la phase d’apprentissage du montage 3D, je dirais 3-4 mois. Cela prendrait certainement moins de temps si je le faisais maintenant.
Êtes-vous entièrement satisfait du résultat final, ou auriez-vous aimé rétrospectivement faire certaines choses différemment ?
Je suis absolument heureux – c’était la première fois que j’essayais de construire un boîtier imprimé en 3D, et avant l’assemblage final, je n’étais pas sûr à 100 % de ce à quoi il ressemblerait. Cependant, après avoir tout assemblé, je n’ai eu qu’une seule pensée : « Wow, c’est solide et ça a l’air vraiment cool ! Je ne pourrais vraiment pas être plus heureux.
Spécifications du PC imprimé en 3D Pinasphere
- CPU: AMD Ryzen 7 5700G
- GPU : AMD Radeon RX Vega11 intégrée
- Stockage: SSD Samsung 980 M.2 de 1 To, SSD Samsung 860 Evo 2,5 pouces SATA de 250 Go
- Mémoire: Mémoire SODIMM DDR4 Corsair Vengeance 3 200 MHz de 16 Go (2 x 8 Go)
- Carte mère : ASRock X300 M-STX
- Bloc d’alimentation : Alimentation externe ASRock 120 W
- Refroidissement: Refroidisseur de liquide Cooler Master MasterLiquid ML120L V2 AIO
Un travail remarquable, Jean. Il s’agit d’un PC personnalisé vraiment unique en son genre : le design est exceptionnel et vous avez également montré que vous pouvez vraiment créer un sacrément beau boîtier de PC imprimé en 3D. aussi.
Cet article a été initialement publié sur Custom PC, qui couvre des configurations étonnantes depuis plus de 20 ans et fait désormais partie de PCGamesN. Rejoignez notre Groupe Facebook de 500 000 membres pour discuter de cette construction.
jeSi vous vous considérez comme un constructeur de PC expert, vous pouvez nous soumettre votre propre version de PC personnalisée dès aujourd’hui pour avoir une chance d’être présenté sur PCGamesN à l’avenir.