Posted at 9:00 a.m.
We will finally know.
At the coach builder Prevost – without accent – in Sainte-Claire, south-east of Quebec, we are about to discover what is the fate of the steel parts first manufactured by Estampro, then incorporated into the fiberglass front face of the coach, during its molding by Elite Composite.
The 3D technical drawing of the mask of the X3-45 coach floats on the screen of mechanical designer René Brunelle, whom Vincent Montembeault, director of strategic sourcing, introduced as “the guy behind the front face”.
René Brunelle enlarges the image, rotates it, shows its details in close-up. He knows the front face better than anyone and than the bottom of his pocket: from the surface defined by the designers, he is the one who designed the elements that make it up, the assemblies that form it.
Stampro’s steel parts appear transparent. Two are used to fix the electric mirrors. Two others retain the wiper mechanisms from the inside. Short threaded rods emerge from it.
“I used it to fix the front face to the structure, until the glue set”, describes René Brunelle.
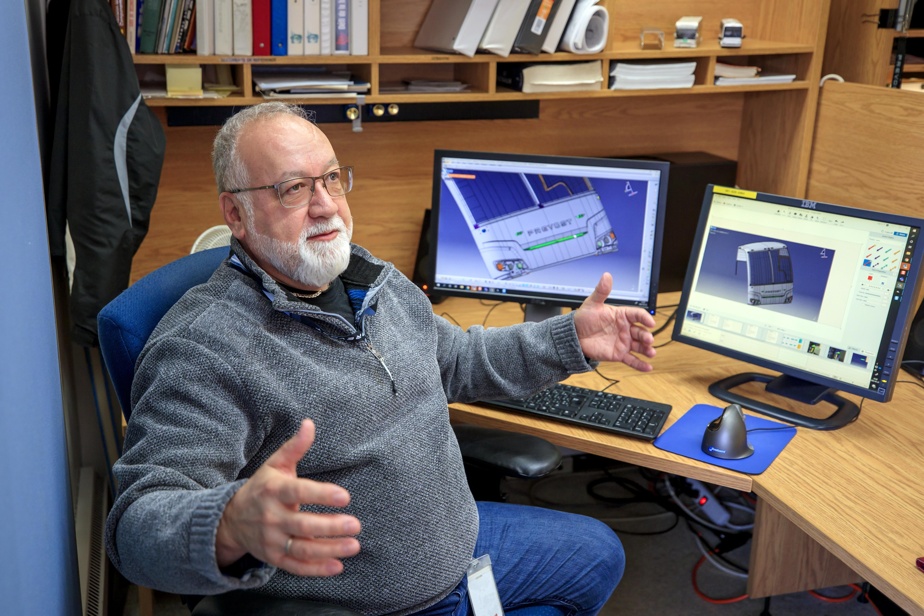
PHOTO ALAIN ROBERGE, THE PRESS
Mechanical designer René Brunelle, in front of the screens showing the technical drawings of the front face of Prevost’s X3-45 coach.
Because it is an adhesive that will definitely retain this mask on the bodywork.
The offices of the engineers and designers are located in the former Prevost factory, itself located opposite the workshop where Eugène Prévost assembled his first coaches, in the heart of the village. In rue Prévost, of course – with an accent, this time.
The town of 3,500 inhabitants has a string of manufacturing companies on the outskirts, several of which manufacture parts for the manufacturer. “We have more than 50 direct Quebec suppliers,” says Vincent Montembeault. With indirect suppliers, we exceed a hundred. »
Factory
The main factory, built in 1980, is located one kilometer further, in the industrial sector.
On either side of its central aisle, as long as two football pitches, about forty deep workstations open perpendicularly, like stalls in a stable – stalls for coaches, however.
In each, a steel carcass goes through a stage of its manufacture. From 25 to 30 coaches are simultaneously being assembled, at different stages of progress.
It is in one of these positions that we find the front panel delivered by Elite Composite.
The large fiberglass shell has been held in a jig to receive the two curved pieces of glass that form its windshield, which an employee is completing the installation.
“Previously, we assembled the front end on the vehicle, and then we put the windshields on,” explained René Brunelle. But the fiberglass face, stiffened by the frame, often had to be touched up to make the glass plates fit perfectly. “We changed the technique on board. We said: we will first assemble the windshields in sub-assemblies, in a conformation template. »
-
PHOTO ALAIN ROBERGE, THE PRESS
The front end is first assembled and then transported on a trolley to the skeleton of the coach.
-
PHOTO ALAIN ROBERGE, THE PRESS
The “stalls” for coaches at the Prevost plant allow the assembly of around thirty vehicles simultaneously, at different stages.
-
PHOTO ALAIN ROBERGE, THE PRESS
The front panel in the final stages of its installation at the Prevost coach factory, established in Sainte-Claire, south of Quebec.
-
PHOTO ALAIN ROBERGE, THE PRESS
The Sainte-Claire plant, built in 1980, now employs more than 500 workers.
1/4
Once properly shod with his glasses, the front face is suspended from a trolley which circulates on a rail fixed to the ceiling. It leads to the next stall, where the skeleton of a coach waits for its mask to be put on.
Its stainless steel structure was welded in a vast workshop to which we do not have access. These wheelless frames are extracted from the stalls by huge motorized carts, which move laterally from one station to another on rails.
In one, what looks like a gigantic roll of aluminum foil is suspended above a car body, ready to unroll the foil which will be put under tension to cover the roof of the vehicle.
In another stall, the finished body will undergo a careful phosphate wash, then it will be transferred to the paint room, where it will receive its primer coat.
The US President’s vehicle was made here. There is Air Force One, but also Ground Force One, the presidential bus.
Vincent Montembeault, Director of Strategic Sourcing
If the H3-45 models are initially intended for the transport of passengers over long distances, the X3-45, slightly lower, will become regional coaches, tour vehicles for artists or motorhomes with deployable sides.
One of these, intended for a private individual, is covered on one of these sides with about forty adhesive butterflies, marking tiny defects of finish which were detected under the white light of an inspection lamp. .
“They will go through each little point, one at a time, with polishers,” says Sylvain Larue, buyer at Prevost. “If the defect requires a touch-up, they will return it to the paint. All vehicles are given the same attention, he says.
Production will ramp up
Currently, the plant’s approximately 550 employees assemble one H3-45 and half an X3-45 per day. Slowed down by the pandemic, production should firm up to two coaches a day during the summer. “We would like to increase to 2.5 vehicles by the end of the year”, specifies Vincent Montembeault.
Precisely, an X3-45 motor home is practically ready to be delivered to a specialist who will do the interior fittings.
Its flanks are covered with multi-coloured swirls in graduated tones. With his hand, project supervisor Stéphane Mercier caresses the smooth surface like a mirror, with no difference in level between the different colors, which nevertheless overlap.
“We do all the colors, we apply three coats of clear varnish, we sand the entire vehicle, then we redo another varnish on top,” he explains. You don’t feel any marks or paint lines. »
Painting a motorhome alone takes 700 to 1,000 hours of work, he says.
“That’s why we need Chabot Carrosserie,” adds Sylvain Larue.
Because the Quebec sector even stretches beyond Prevost, as we will discover next week.
Learn more
-
- 1924
- Year in which cabinetmaker Eugène Prévost began manufacturing wooden bus bodies mounted on REO truck frames, marking the founding of the company that bears his name. Prevost has been part of the Volvo Group since 2004.
source: Prevost