In February 2023, during one of the first flights of a Southwest Airlines Boeing 737 Max, a failure of the automatic stabilizer forced the pilot to make an emergency landing shortly after takeoff.
Two months later, an Alaska Airlines 737 Max with eight hours of flight time was briefly grounded by a malfunction in the fire detection system. In November, an engine on a brand-new United Airlines 737 Max failed at 37,000 feet.
These incidents, reported by carriers to the Federal Aviation Administration, did not make headlines. They appear not to have put anyone in danger and it is not clear who is responsible. But since January 5, when an Alaska Airlines 737 Max 9 lost a panel in mid-flight, previous incidents have taken on new significance and raised questions about the quality of Boeing planes.
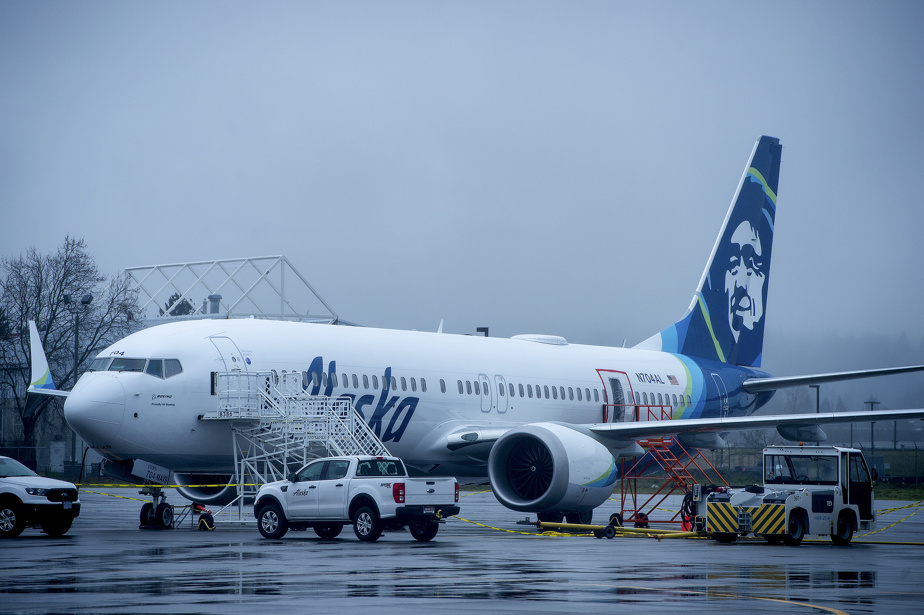
PHOTO AMANDA LUCIER, THE NEW YORK TIMES ARCHIVES
On January 5, this Alaska Airlines 737 Max 9 lost a panel in mid-flight.
“There are a lot of areas where things don’t seem to be done right at the factory,” said engineer and aviation safety expert Joe Jacobsen, who spent more than a decade at Boeing and more than 25 years at the FAA.
It seems like there are shortcuts everywhere; work not done properly.
Joe Jacobsen, engineer and aviation safety expert
Interviews with aviation safety experts and numerous current and former Boeing employees paint a disturbing picture of a company long considered the pinnacle of American engineering. They suggest Boeing is struggling to improve quality after two 737 Max 8 crashes in 2018 and 2019 killed nearly 350 people.
Some of the crucial layers of redundancies that keep Boeing’s planes safe appear not to be enough, these people say. The experience level of Boeing staff has fallen since the start of the pandemic. The inspection process supposed to monitor the work done by its mechanics has been weakened over the years. And some suppliers are struggling to meet both the quality standards and production rates imposed by Boeing.
Leadership changes
Wanting to show regulators, airlines and passengers that it is taking its latest crisis seriously, Boeing announced sweeping management changes Monday. CEO Dave Calhoun will leave at the end of the year, and Stan Deal, director of the commercial aircraft division – which builds the 737 Max – has been retired. Board Chairman Larry Kellner has resigned from his position and will not seek re-election to the Board
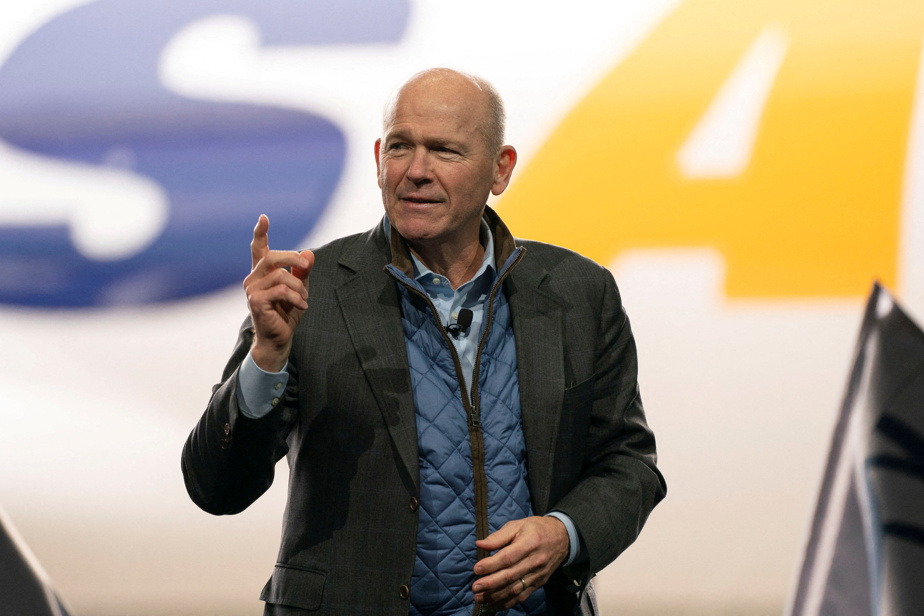
PHOTO DAVID RYDER, REUTERS ARCHIVES
Boeing CEO Dave Calhoun will step down at the end of the year.
When he was named CEO in January 2020, Mr. Calhoun pledged to improve Boeing’s safety culture. Members with engineering and safety expertise were appointed to the board, which now has a safety committee. According to Boeing, the number of quality inspectors assigned to commercial aircraft has increased by 20% since 2019 and there are more inspections per aircraft.
After the two 737 Max 8 crashes, Boeing and regulators focused on their direct causes: design flaws and faulty software. But, according to some current and former employees, construction problems were just as apparent and Boeing executives and regulators should have noticed.
After the Jan. 5 crash, a six-week FAA audit of 737 Max production found dozens of quality control deficiencies at Boeing. The FAA gave Boeing three months – until the end of May – to fix these problems.
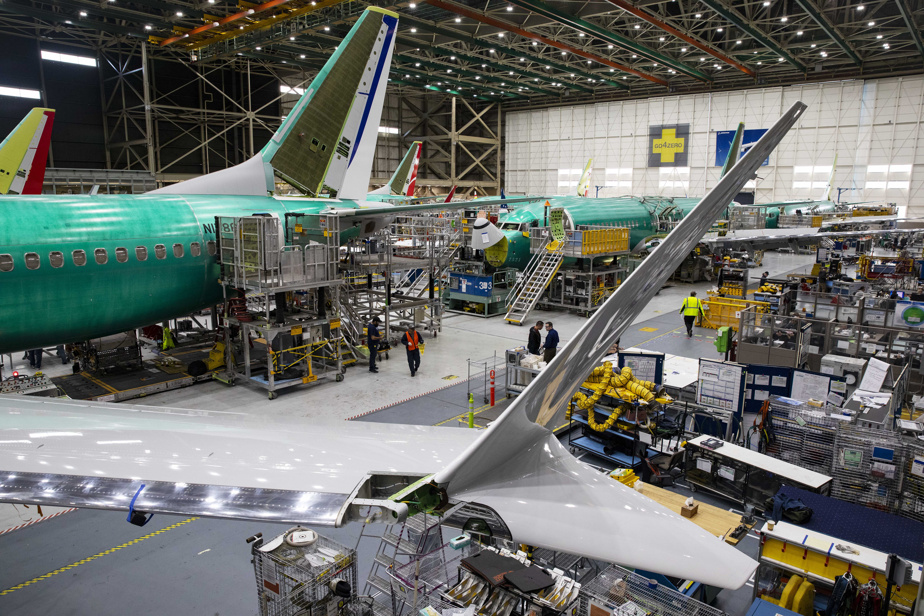
PHOTO RUTH FREMSON, THE NEW YORK TIMES ARCHIVES
Boeing 737 Max 8 under construction at Renton, Washington assembly plant
The National Transportation Safety Board has identified the source of the event where a 737 Max lost a panel in flight: during assembly at the Boeing factory in Renton, Washington. This panel was removed, then reinstalled without the bolts supposed to secure it to the fuselage. This panel (a “door stopper”, in aeronautical jargon) is used to close the space left by an unnecessary emergency exit.
According to current and former Boeing employees, the event illustrates long-standing problems. They talk about high production rates putting assemblers under intense pressure and sometimes leading to questionable practices, making them fear a deterioration in quality and safety.
Davin Fischer, a former mechanic from Renton, believes the company culture changed around 2017, when Boeing launched the Max: “They were trying to increase the speeds and kept pushing to go faster, faster, faster . »
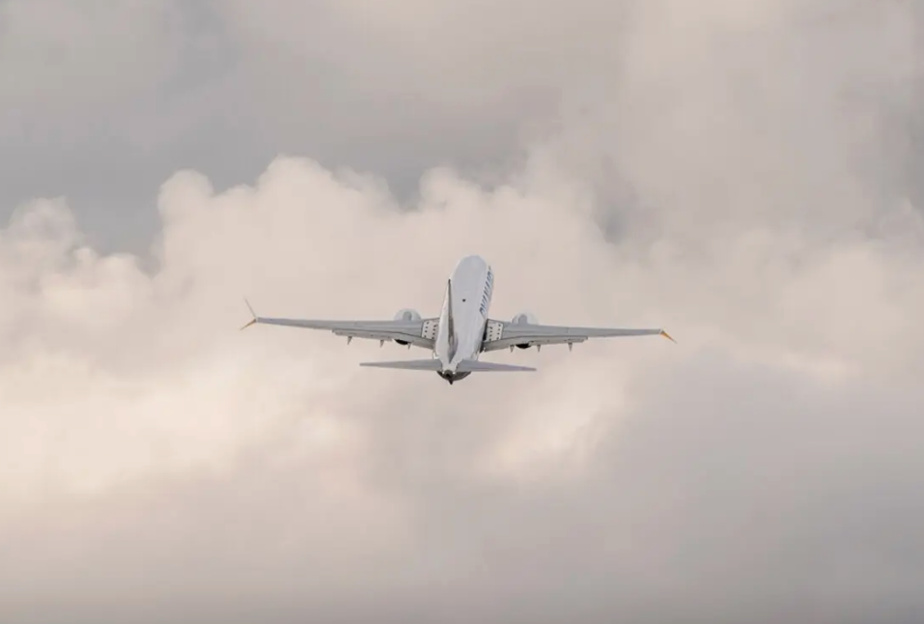
PHOTO DAVID RYDER, BLOOMBERG ARCHIVES
Boeing 737 Max taking off in Renton, Washington
The Max was launched in response to a new fuel-efficient aircraft from Airbus. Boeing increased production from about 42 Max jets per month in early 2017 to about 52 in 2018. Production fell to virtually zero after the second crash, in Ethiopia, when regulators around the world grounded the plane. ground. The plane returned to service at the end of 2020 and Boeing began increasing production rates again to avoid falling further behind Airbus.
“This must change”
Today, some Boeing executives admit mistakes.
“For years, we prioritized the number of planes coming out of the factory instead of doing things the right way, and that has to change,” said financial director Brian West, during a meeting with investors last week.
Mr. Calhoun acknowledges that Boeing needs to do better, but he defends the company’s approach to production. “Over the past few years, we have been careful not to push the system too much, and we have never hesitated to slow down, reduce throughput or stop deliveries to take the time required to do things right,” said he declared in January.
Current and former Boeing employees, most of whom spoke on condition of anonymity to protect their careers, gave examples of declines in quality over the years. Many of them still say they respect Boeing, and want it to succeed.
A current worker at the factory that produces the 787 Dreamliner in North Charleston, South Carolina, says he has seen numerous problems during assembly, including improperly routed cables in the wrong places, increasing the risk of friction and damage.
Sometimes employees “shop their inspector,” to find someone who would approve the work, the worker said.
Some concerns echo accusations of quality lapses made by sources at the Boeing South Carolina plant who spoke to the New York Times in 2019.
According to several current and former employees at the North Charleston and Renton aircraft factories, mechanics building planes were allowed in some cases to sign off on inspections of their own work. Such “self-verification” removes a crucial layer of quality control, they said.
In a statement Wednesday, Boeing said it eliminated self-inspection in South Carolina in 2021 and that the practice represented less than 10% of inspections at other sites. The company inspects each plane before delivery to ensure wiring harnesses are properly spaced, the release said, and it does not allow anyone to shop its inspector.
The shock of COVID-19
Another recent factor is assembler experience, which has been declining since the pandemic.
When COVID-19 hit in March 2020, air travel collapsed and many aviation executives believed the industry would take years to recover. Boeing cut jobs, bought back positions and encouraged early retirement. Ultimately, 19,000 employees left Boeing, some of whom had decades of experience.
Boeing today employs 171,000 people across its commercial aviation, defense, services and other divisions. This is 20% more than in 1er January 2021. But the new workers have less experience, current and former employees note.
A former quality inspector at the Renton plant who left in 2023 said training for new employees was sometimes insufficient, with crucial skills sometimes learned on the job from more experienced colleagues.
Since Jan. 5, Boeing says, employees have been asking for more training, and the company has been working to meet those needs, including adding training at factories starting this month.
This article was published in the New York Times.
Read this article in its original version (in English; subscription required)