Who ?
Agapyo has its origins in the design of a material by Mike Thompson, a professor of chemical engineering at McMaster University in Ontario. Through research, the scientist identified elements in wood pulp that could – once transformed – lead to a material that could replace ABS plastic, the popular polymer with many applications.
Since then, the Montreal startup – officially registered in 2023 – has acquired the exclusive license to develop and market the technology. Its goal: to replace ABS plastic in order to reduce greenhouse gas emissions and the disposal of contaminants resulting from the consumption of the polymer.
“Right now, we’re in this beautiful moment where we’re making the transition from the lab to commercialization,” summarizes Alina Grenier-Arellano, vice president of business development. She shares the title of founder with Monika Rak, a scientist responsible for the technological development of the material.
The product
The product Agapyo is developing – called JAM – is a bioplastic made from a carbohydrate found in wood pulp. “We use a product from the forest industry that has been the least processed and has properties that are closest to the tree,” she says.
The organic compound extracted from the wood pulp makes it possible to obtain a rigid, biodegradable material, which has performances similar to those of ABS plastic, specifies Mme Grenier-Arellano. “But also and above all, it is a material that has very interesting particularities. It can be produced on a large scale and can be molded, which is not the case with other bioplastics,” she says.
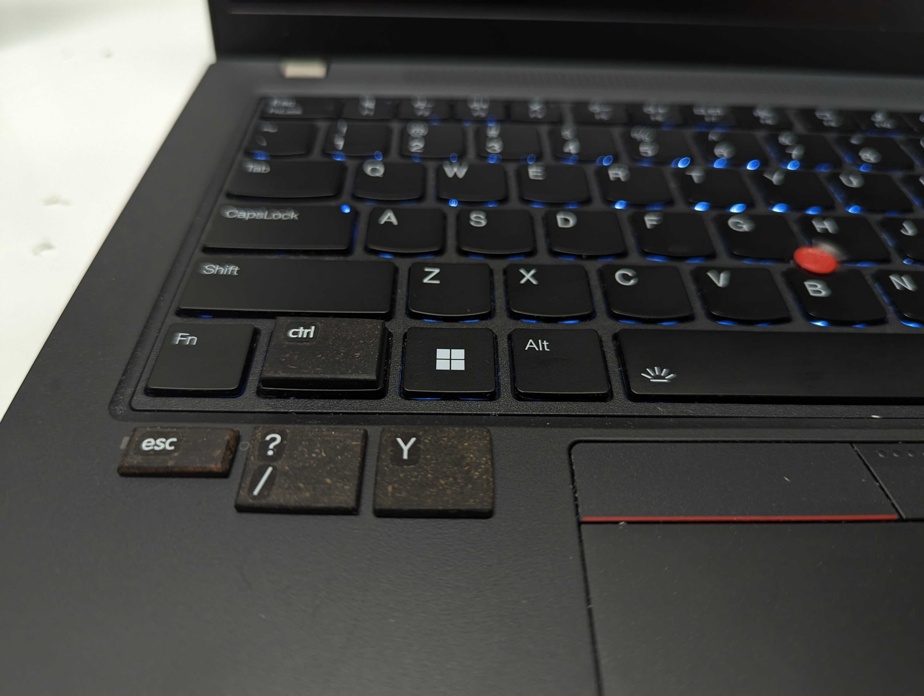
PHOTO PROVIDED BY AGAPYO
The product that Agapyo is developing – called JAM – is a bioplastic made from a carbohydrate present in wood pulp. It can be used, among other things, to make computer keys.
“If our material replaced all the ABS that exists, it would represent between 1% and 2% of what comes out of the forest industry. We have the capacity to do it,” she replies. JAM’s production could come mainly from forest industry residues such as unused sawdust from sawmills or non-recycled cardboard.
The challenges
The challenge for Agapyo lies in its ability to carve out a place for itself in the production chain of products consumed daily. “We have to succeed in getting all the stakeholders involved in the development and production of a product – the major manufacturers, but also the subcontractors and the companies with which we develop the material – to coordinate,” summarizes Alina Grenier-Arellano.
The future
“Our mission is for JAM to replace the plastics we use every day on a global scale,” she says optimistically. In recent weeks, a good quantity of bioplastic has been produced. This will allow samples to be made to test its industrial use with existing customers, including Samsung.
In the coming months, Agapyo will focus its development on the electronics and computer products market. “We are considering other products that we use in our homes, such as toys or household appliances, or even the automotive sector… but eventually. Not right away.”