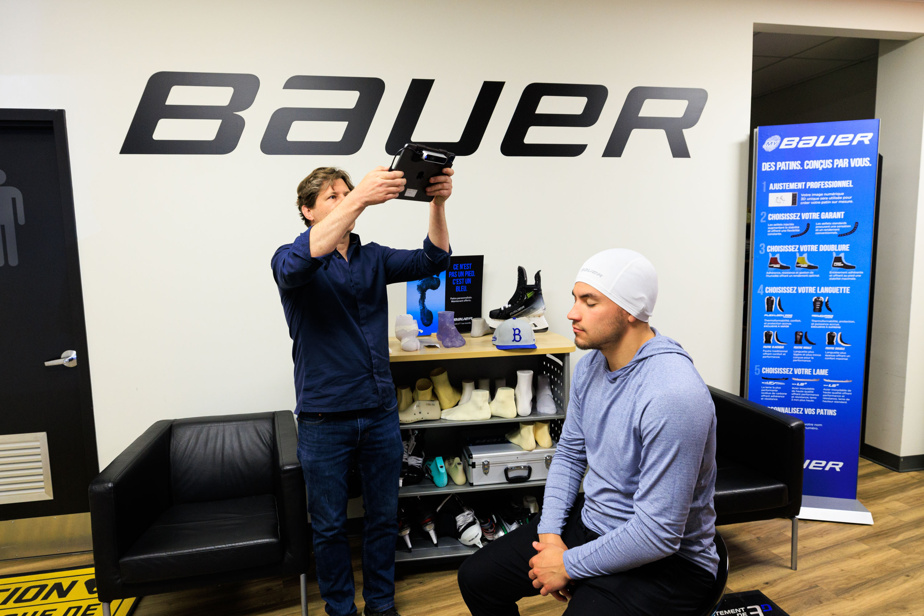
PHOTO HUGO-SÉBASTIEN AUBERT, THE PRESS
Mathieu Desjardins, category manager – protective equipment, collects the data. This technology has been offered for two seasons to professional players, and since last season to sporting goods retailers.
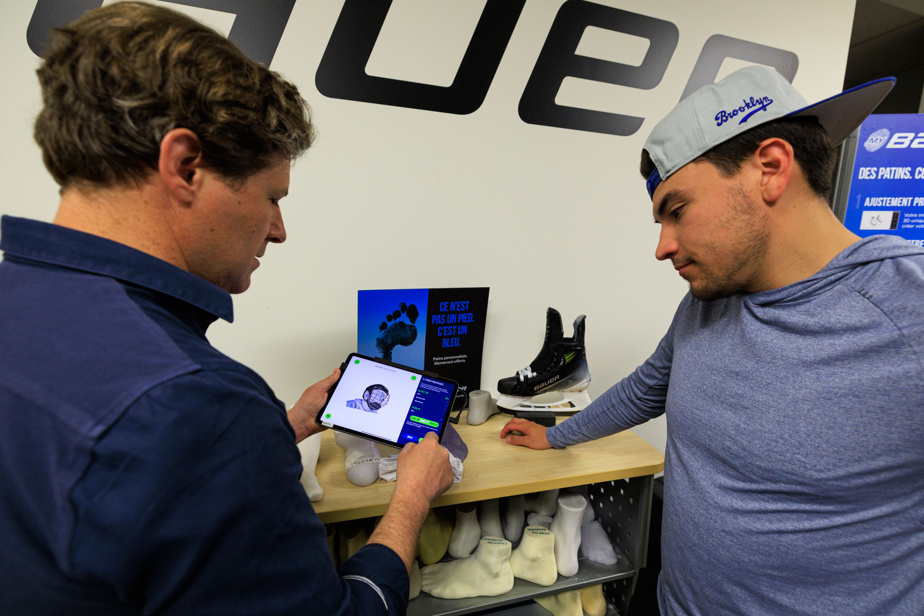
PHOTO HUGO-SÉBASTIEN AUBERT, THE PRESS
Nick Suzuki observes the results of the scan.
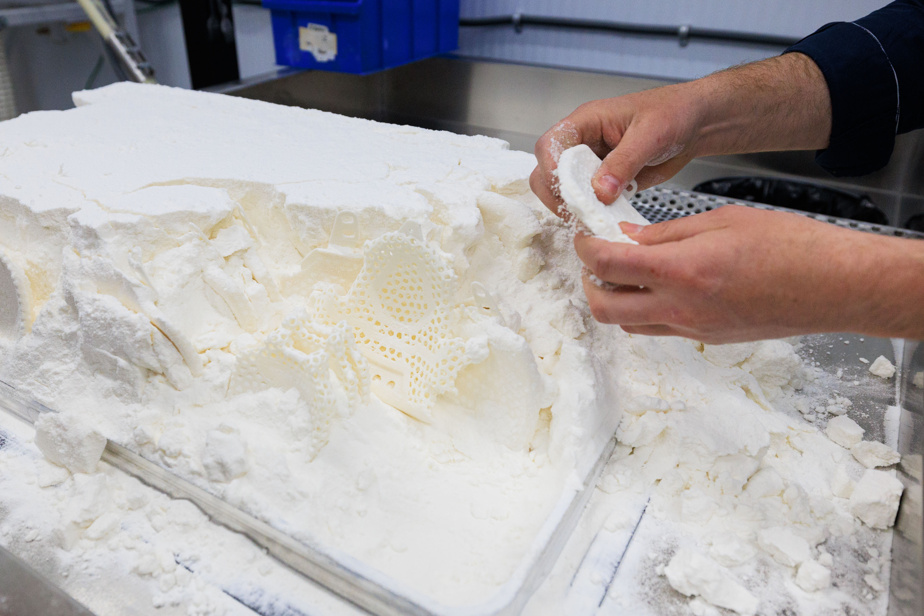
PHOTO HUGO-SÉBASTIEN AUBERT, THE PRESS
In the 3D printer, thin layers of plastic powder are deposited one by one. A laser melts them according to the pattern obtained by the digitization. Twenty hours are needed to produce a batch of 20 custom helmet padding. At the end of this process, a thick “cake” is extracted from the printer.
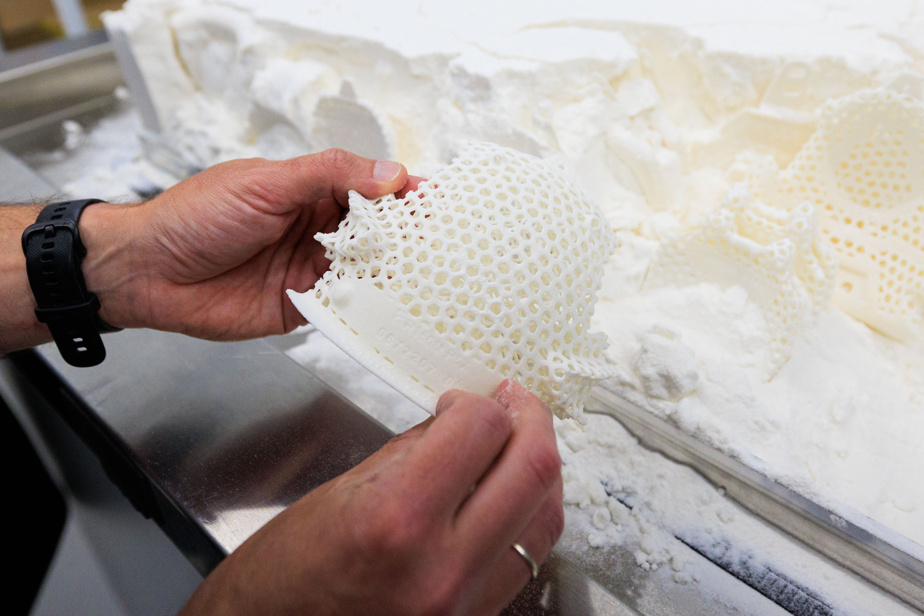
PHOTO HUGO-SÉBASTIEN AUBERT, THE PRESS
We release the pieces of padding from the “cake”. Residual powder can be reused.
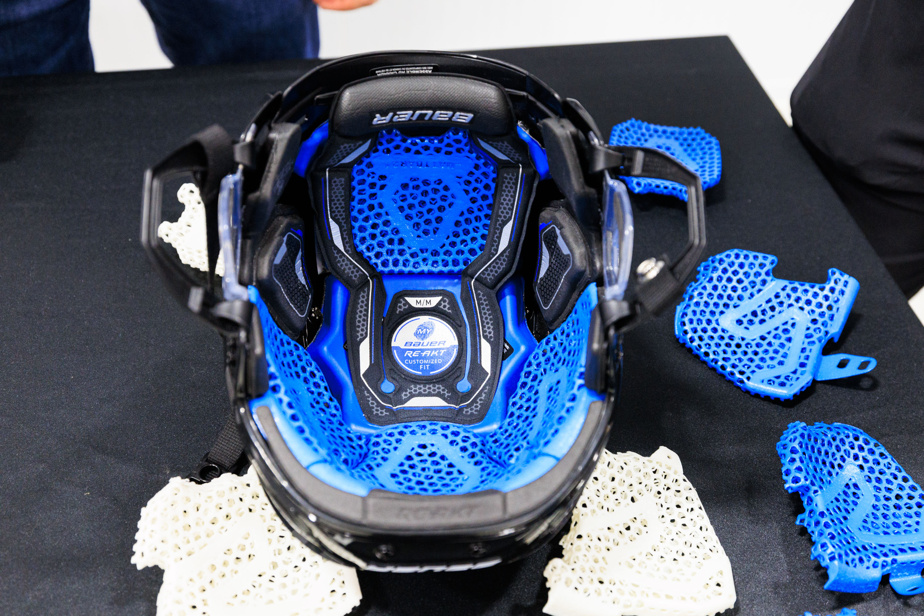
PHOTO HUGO-SÉBASTIEN AUBERT, THE PRESS
The upholstery pieces are then polished and stained, then placed in a shell. The first players to test this customization technology were Cale Makar and Jack Eichel. At the Habs, Paul Byron then, more recently, Cole Caufield and Nick Suzuki took advantage of it.
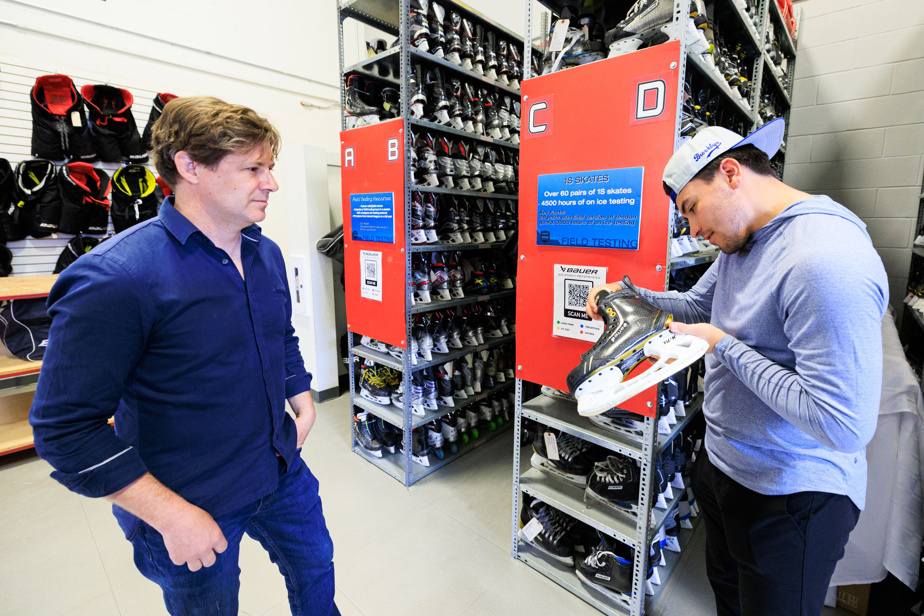
PHOTO HUGO-SÉBASTIEN AUBERT, THE PRESS
At its innovation center in Blainville, Bauer keeps pieces of equipment from previous generations. Research and development engineers can thus study old models that are 15 to 20 years old. Within moments, Nick Suzuki found the skates he wore in minor hockey.
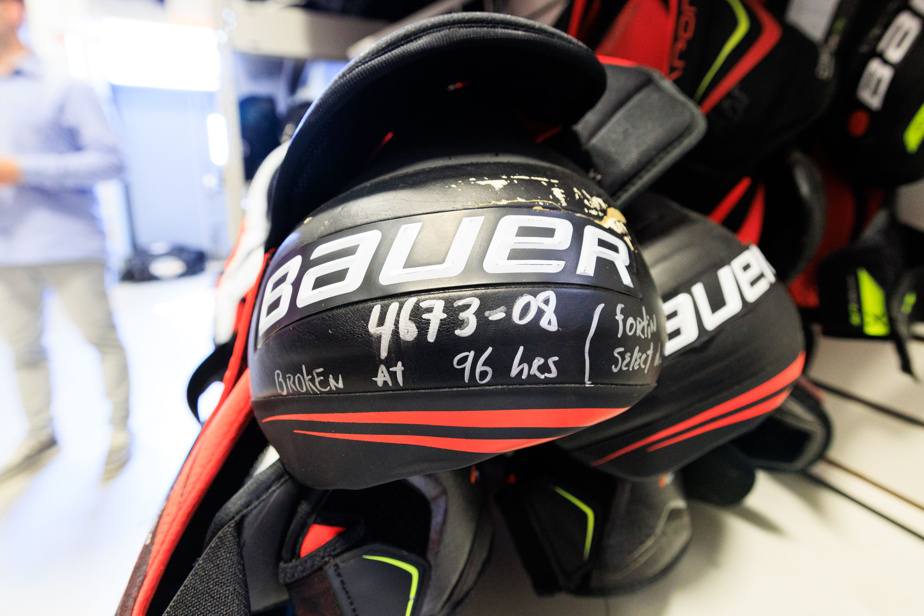
PHOTO HUGO-SÉBASTIEN AUBERT, THE PRESS
Parts that failed stress tests are also retained. For example, this pair of shoulder pads that split after 96 hours of testing.
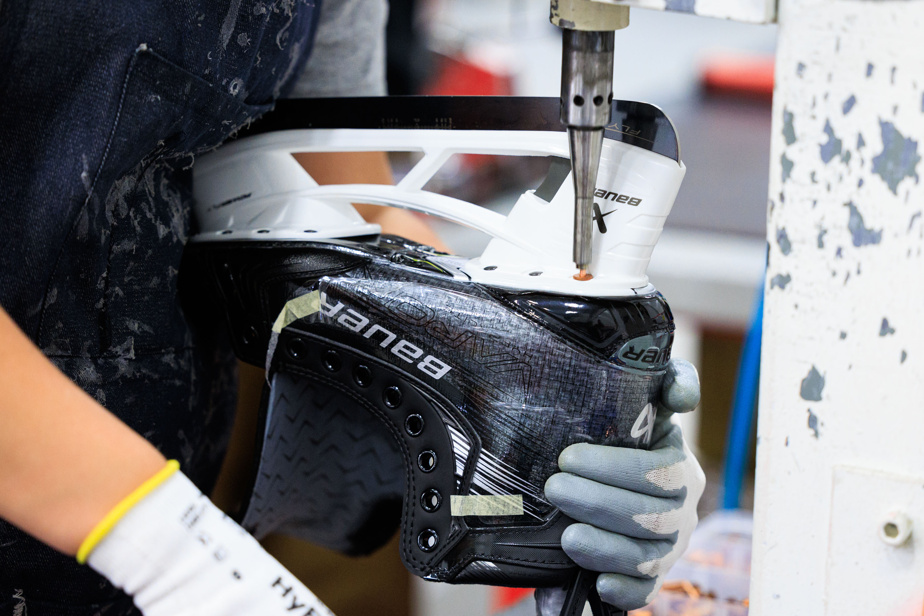
PHOTO HUGO-SÉBASTIEN AUBERT, THE PRESS
Visit of the skate manufacturing area, where about fifty people work
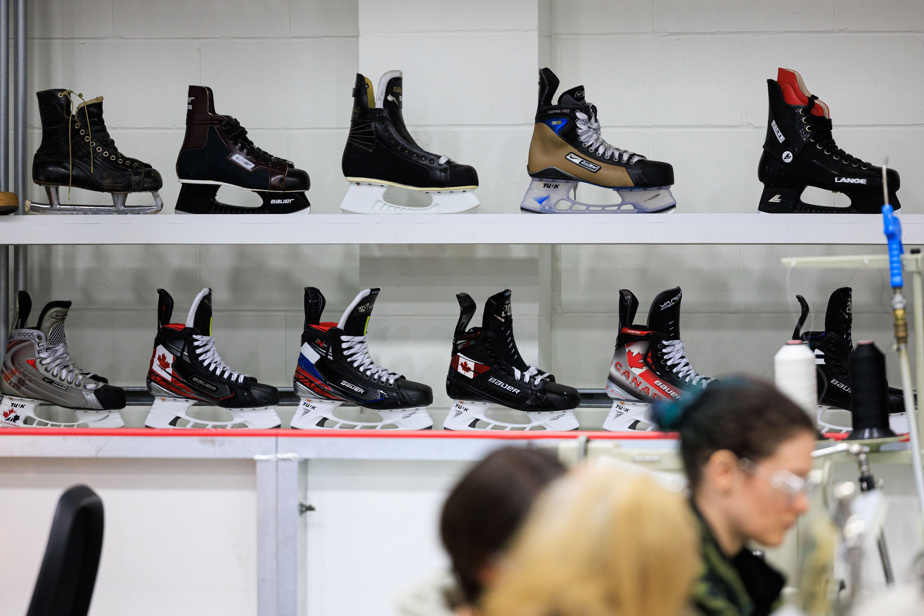
PHOTO HUGO-SÉBASTIEN AUBERT, THE PRESS
The vast majority of Bauer skates are made in Asia. However, the Blainville plant produces some 20,000 pairs a year. These are mainly intended for professional players.
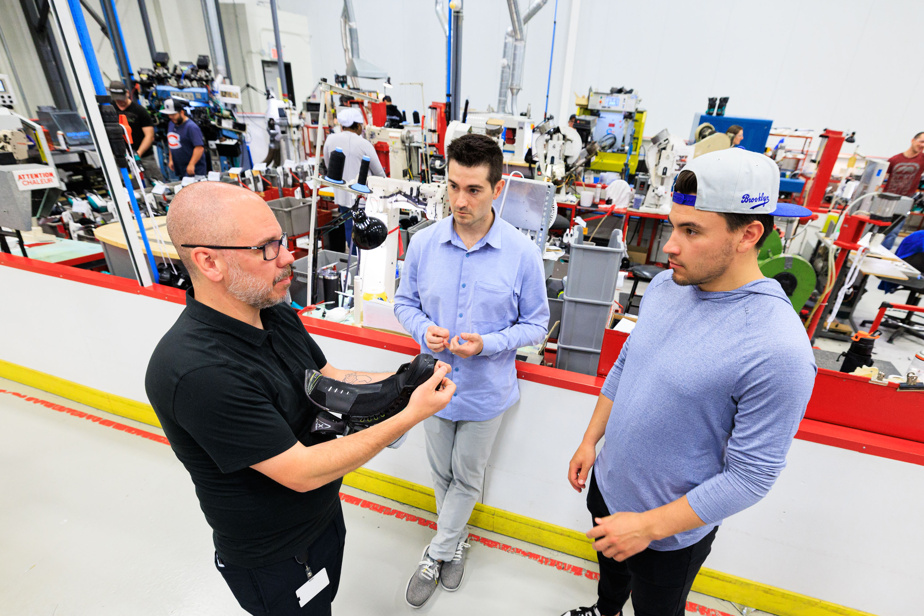
PHOTO HUGO-SÉBASTIEN AUBERT, THE PRESS
Nick Suzuki chats with Patrick Jarry, production manager (in black), and Justin Bonitatibus, representative with a few NHL teams, including the Canadiens. Nick Suzuki takes advantage of his visit to point out that, last season, the insole of his skates was too narrow compared to the boot.
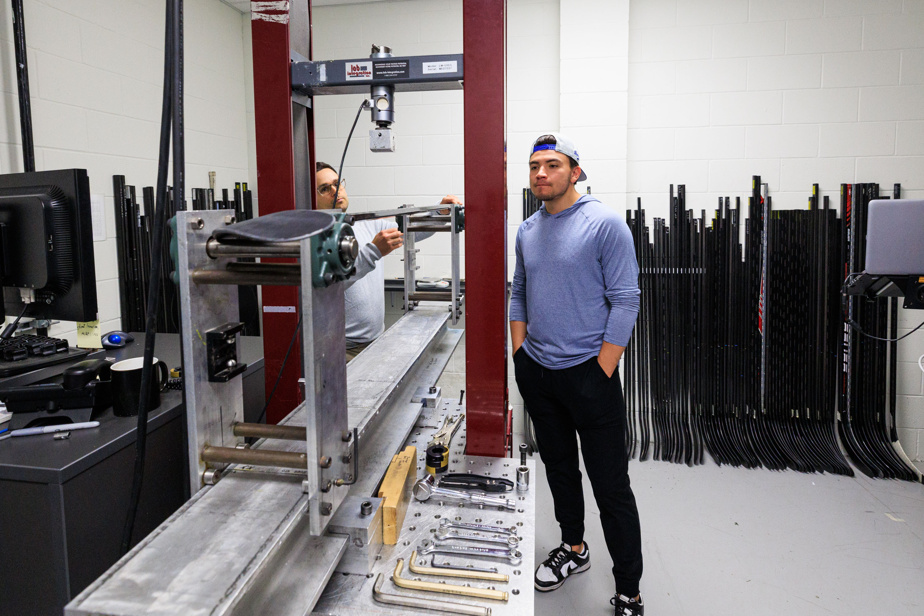
PHOTO HUGO-SÉBASTIEN AUBERT, THE PRESS
Marc-André Dickey, laboratory technician, presents the stick personalization devices. “I hardly ever change anything in my equipment,” Nick Suzuki later explained. I’ve tried different sticks over the years but always come back to the same one I was already using in juniors. Athlete Services Manager Henry Breslin (not pictured) points out that players can tell in seconds if a stick is even a few grams over the desired weight.
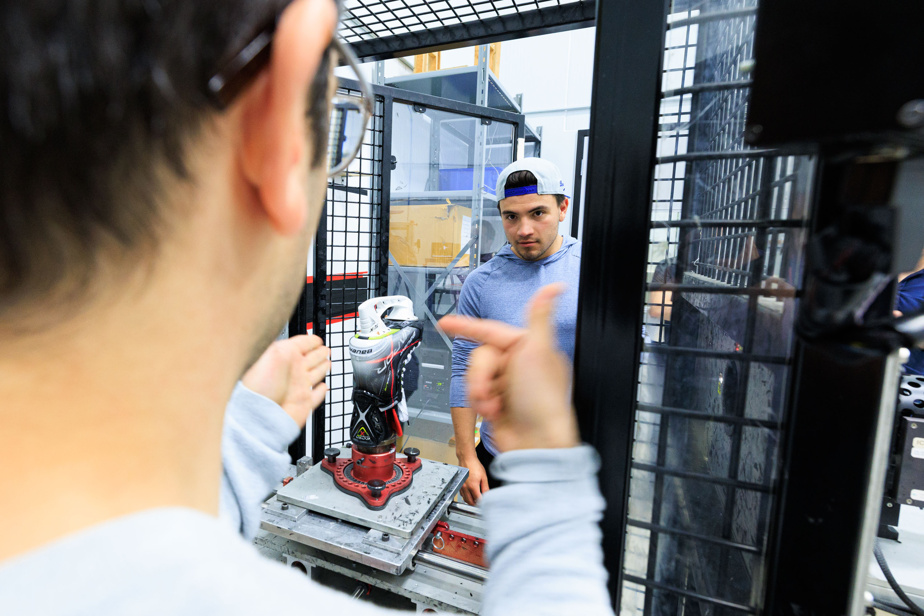
PHOTO HUGO-SÉBASTIEN AUBERT, THE PRESS
Last stop: the impact test room. A puck thrower throws a disc at more than 130 km/h on a skate (our photo). “I received some like that,” sneers the Canadiens center player. A little further on, another device simulates side impacts on a helmet. Although no equipment manufacturer can assure athletes that a helmet will protect them 100% from a concussion, the entire internal structure of the helmet is designed to absorb as much energy as possible.