(GIVE, Denmark) The wind industry, responsible for hundreds of thousands of turbines producing clean electricity, was born in a notoriously windy region of Denmark, Jutland.
It was here, nearly 50 years ago, after the 1973 oil embargo cut supplies to the West, that inventors and machinists began to exchange ideas on how to exploit the wind that sweeps across this flat expanse separating the North Sea from the islands that form the rest of Denmark. While countless people have perfected these propeller machines that stand on coasts, plains and mountains, none has had more influence than a Jutlander named Henrik Stiesdal.
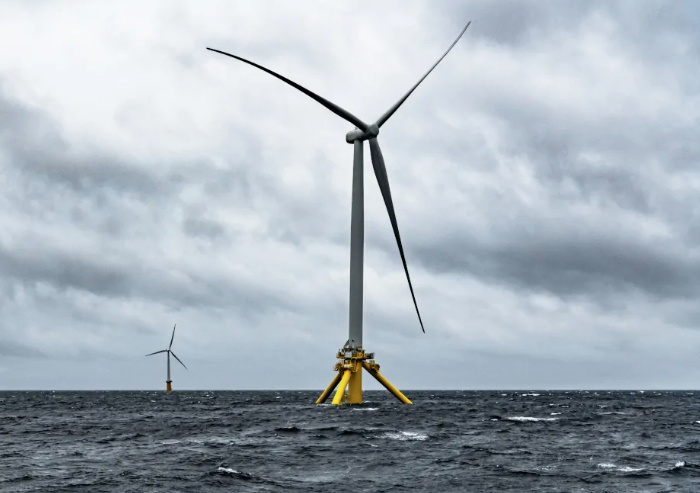
PHOTO FROM STIESDAL WEBSITE
A fully functional prototype of a Stiesdal TetraSpar floating foundation has been installed since June 2021 10 km off the Norwegian coast in the North Sea. It carries a 3.6 MW wind turbine from Siemens Gamesa.
At 21, he built a rudimentary wind turbine to light his parents’ farm. Later, he co-designed a three-bladed rotor that spawned a multi-billion dollar global industry. His inventions have given rise to a thousand patents, and Henrik Stiesdal is recognized as a pioneer in this very Danish field of expertise.
At 66, he continues. After working for 40 years for companies that have become today’s wind energy giants, Mr. Stiesdal launched a start-up that bears his name. He works on innovative ways to produce clean and affordable energy, while fighting climate change.
At its factory in Give, a small town in the middle of Jutland, welders are assembling huge tetrahedral structures, designed by Mr Stiesdal, which will carry floating wind turbines. Made of tubes and resembling huge Lego toys, these semi-submersible foundations bear the name TetraSpar. A fully functional prototype has been installed since June 2021 10 km off the Norwegian coast. The structure covers an area equivalent to two football pitches.
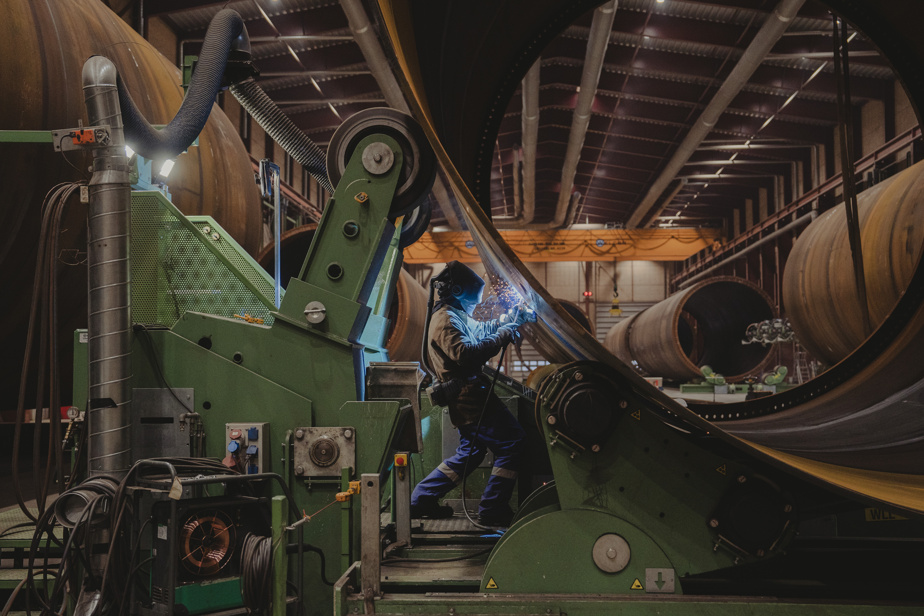
PHOTO CHARLOTTE DE LA FUENTE, THE NEW YORK TIMES
In the Stiesdal factory in Give, a small town in the middle of Jutland, welders are assembling huge tetrahedral structures, designed by Henrik Stiesdal, which will carry floating wind turbines.
Nearby, engineers are testing a machine that looks like a series of stacks of cafeteria trays. It is a prototype electrolyser, a device that takes water and extracts hydrogen, a gas called to replace fossil fuels.
CO capture2
Two hours to the north is another prototype: an industrial oven called SkyClean, which cooks agricultural waste – such as manure and straw – preventing its carbon content from escaping into the atmosphere and forming carbon there. carbon dioxide.
This big, outspoken guy isn’t afraid to work with hydrogen – an explosive gas – in his basement. Stiesdal is betting that its technologies will significantly reduce greenhouse gas emissions. He’s also keen to keep Denmark and northern Europe at the forefront now that funding for the energy transition is increasing to wean the world off fossil fuels.
Mr. Stiesdal is getting involved as the renewable energy industry in Northern Europe is in the doldrums.
Major wind turbine makers in the region – including his former employer Siemens Gamesa Renewable Energy – are struggling due to rising costs and slow project approvals. It is feared that the Chinese, who have already monopolized the manufacture of solar panels, will do the same in wind power.
Mr. Stiesdal has raised around $100 million for his company from a small group of investors. His family owns around 20% of the company, which employs 125 people. In order to cut costs and focus on innovation, he wants to license his new products, leaving the manufacturing to others.
After retiring from Siemens Gamesa, where he was chief technology officer, Mr. Stiesdal looked for new projects. He turned to floating wind turbines, which provide access to waters too deep for wind turbines placed on the seabed. Floating wind turbines make it possible to exploit large areas far from the coast, but they are more expensive, in particular because they are not produced on the chain. Mr Stiesdal wants to change that.
Wind turbines anchored 200 m deep
Copenhagen Infrastructure Partners co-financed a prototype floating base wind turbine called TetraSpar, designed by Mr. Stiesdal.
This design would be used for future wind farms, notably off Eureka, in northern California. The TetraSpar floating foundation prototype has been fully functional for a year. It is anchored off the coast of Norway, in a depth of 200 m, and carries a 3.6 MW wind turbine from Siemens Gamesa.
“Henrik’s primary goal is that floats can be produced intelligently,” says Torsten Smed, co-founder of Copenhagen Infrastructure Partners. This means in series, and in such a way that the parts of the structure, then the turbine, can be assembled seamlessly from the quay. Everything is then towed out to sea to the wind farm, miles offshore.

PHOTO FROM STIESDAL WEBSITE
The floats are mass-produced, then moved to a dock where the structure is assembled before perching a wind turbine on it. The assembly is done without soldering.
The company is manufacturing these structures in Jutland for a future wind farm off Scotland. It uses robots and other technologies to stay competitive despite the high cost of labor in Denmark.
Green hydrogen production
Along with researchers at the Technical University of Denmark, Dr. Stiesdal is also developing electrolysers to reduce the high cost of producing green hydrogen (a zero-emission product). Climatologists and industrialists believe that hydrogen will be needed to power heavy industries, such as steel, and as fuel for planes and trucks.
His electrolysers are still in the trial stage, but Mr. Stiesdal has already struck a manufacturing deal with Reliance Industries, an Indian energy giant.
He is also building a large-scale version of SkyClean, his carbon capture machine, which uses heat to fix carbon from agricultural waste into charcoal-like pellets.
Mr. Stiesdal’s company, like many start-ups, is losing money, but he predicts profitability by 2024. He believes he will succeed because his technologies are suited to a small country like Denmark, which has less of 6 million inhabitants.
The products are not very high-tech and not very labor intensive: they are based on a hands-on approach and a well-trained workforce from an accessible university system.
“In many ways, they resemble my first innovations 45 years ago. »
This article was originally published in the New York Times.