The Laval company Bedcolab has invested nearly six million dollars over the past five years to begin the shift towards a 4.0 factory and increase its production capacity. A strategy based on caution, in order to face the many challenges of its industry.
Posted at 10:00 a.m.
Specialized in the design, manufacture and installation of laboratory furniture and fume hoods for research centers, universities, pharmaceutical companies and multinationals such as Pepsi, Bedcolab operates in a niche market. There aren’t many competing companies, but the stakes are high. “We do about 150 projects a year, and it’s never the same thing. Our order book is full until 2023, but we do not know what is coming. Our customers are the contractors, and we don’t tolerate any delay in delivery so as not to delay construction sites,” says Stéphane Lefebvre, the company’s general manager.
MUHC, CHUM and Dow Chemical
In 2012-2013, Bedcolab worked on the projects of the McGill University Health Center (MUHC) and the University of Montreal Hospital Center (CHUM), where the challenges were numerous. Once that turbulent period passed, the company took on the contract for the largest laboratory ever built in North America, the Dow Chemical Innovation Center in Lake Jackson, Texas. Once again, the challenges were multiple, but above all they brought about reflection and an organizational overhaul.
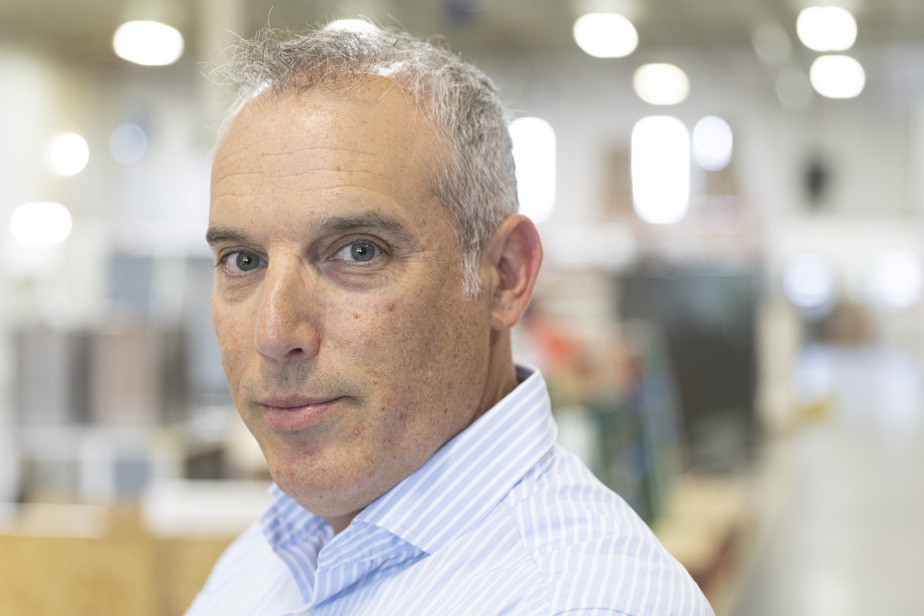
PHOTO PHILIPPE BOIVIN, THE PRESS
Stéphane Lefebvre, Managing Director of Bedcolab
We have developed a strategic plan to avoid a roller coaster in our sales and eliminate plant production stoppages. We have integrated new distributors. As a result, our market has changed, we have gone from 20% of our turnover in the United States to 65%.
Stéphane Lefebvre, Managing Director of Bedcolab
Investing in people and machines
The prospects of a recession, the scope of the projects and above all the need for a specialized workforce are the other drivers of the changes that have occurred. “During our first phase, we invested in human capital, whether in terms of hiring, training, improving spaces, etc. “explains the general manager.
Next step, factory 4.0
After humans, Bedcolab focused on automation. Since 2018, it has added its first collaborating robot, a “servo-electric panel” bender and has overhauled its digital infrastructure. “Before, we simply couldn’t send our employees to work from home because of cybersecurity issues. Two months before the pandemic, that would have been even impossible. We invested just in time, but it represents a lot of work. It’s a bit like putting fuel in a moving plane”, illustrates the leader.
A family business, Bedcolab can count on the contribution of a third generation that is evolving within the organization. It has big plans, like expanding the plant by 25,000 sq.2. An investment estimated at more than two million dollars. “We are waiting for the permits and we hope to break ground in 2023,” says Stéphane Lefebvre.
In the meantime, Bedcolab continues to invest, while its market is growing. “Other investments will be necessary to further increase our production capacity and to reduce our dependence on trades doomed to disappear. We are not short of customers, but we want to balance our product portfolio. This means moving towards the next stage, the 4.0 factory where the computer systems will be fully integrated to allow us to operate continuously. »