Présage
Nous ne cachons pas notre affection pour le véhicule électrique ici à Ars, et cela va au-delà des voitures et des camions légers que nous conduisons et écrivons habituellement. Le secteur des véhicules commerciaux est également électrisant, mais la plupart de ce que nous avons vu en termes de véhicules électriques commerciaux se situe soit à l’extrémité la plus légère de l’échelle – des camions de classe 2 comme le Ford E-Transit et le BrightDrop Zevo 600 – soit le plus gros des camions de classe 8 comme nous en avons vu chez Daimler, Volvo et Tesla.
Mais qu’en est-il d’un juste milieu ? L’une des premières entreprises à s’attaquer aux véhicules électriques commerciaux manquants entre les deux extrémités du spectre est Harbinger, qui a développé sa propre plate-forme pour les véhicules électriques de classe 4 à 7. Il a récemment lancé une nouvelle plate-forme de camions électriques de poids moyen conçue pour la livraison du dernier kilomètre. Harbinger a conçu le groupe motopropulseur en interne dans un souci de durabilité.
« Quand nous regardons le plus gros produit de notre segment – pour les véhicules de livraison de toute façon – c’est le Ford F-59, qui est un châssis dépouillé, et c’est essentiellement un moteur avec un minimum de choses supplémentaires », a déclaré le PDG de Harbinger, John Harris, à Ars. « C’est le même moteur que Ford mettra dans un F-250. Le moteur a la durabilité, il peut être monté et manipulé correctement, et il n’y a pas grand-chose d’autre là-bas. Mais si nous regardons un EV, c’est très différent. Sa batterie emballe plus que le groupe motopropulseur. Et Ford n’a pas de boîte à outils à usage moyen pour l’électrification.
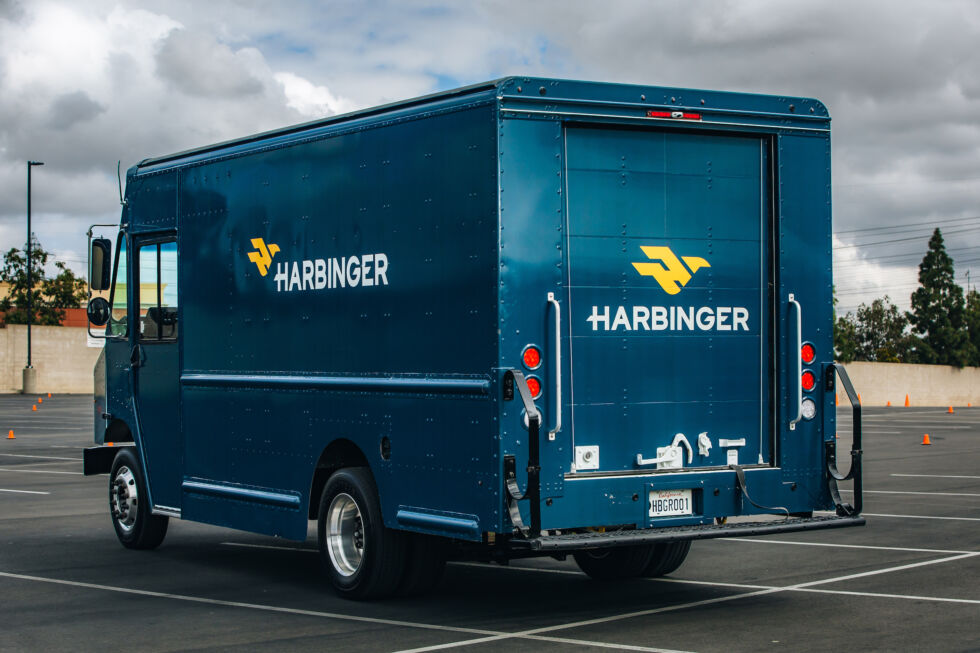
Présage
L’un des problèmes est une clientèle qui s’attend à tirer pleinement parti de ses camions. « Quand vous regardez ce que nous construisons, personne n’est d’accord avec le camion de classe 4-6 à moins qu’il n’ait une durée de vie de 15 à 20 ans », a déclaré Harris. « Chez UPS, tous les véhicules sont sur la route depuis 20 ans. Il n’est pas rare qu’ils arrivent à 25 ans. Et parfois, ils remplacent les moteurs de ces véhicules en 15 ans, mais tout le reste est toujours bon, donc ça vaut le coup. Alors ici, lorsque nous examinons chaque élément de la technologie, nous adoptons une approche différente pour atteindre cette durabilité. » Par conséquent, la plate-forme de Harbinger est conçue pour une durée de vie de 20 ans et 450 000 milles (724 203 km).
Par exemple : la batterie. Dans une voiture de tourisme EV, la batterie est généralement construite à partir de composants en acier estampé, scellés avec un scellant pour carrosserie. C’est génial pour la production de masse, selon Harris, « mais quand vous regardez une batterie Tesla qui a 15 ans, et il y en a quelques maintenant, les cellules vont bien, les boîtiers sont tous rouillés. »
Harbinger a opté pour une conception modulaire qui utilise 2170 cellules cylindriques, emballées par incréments de 35 kWh, chacune ajoutant environ 40 miles (64 km) d’autonomie. Au lieu d’emboutir le boîtier du pack en acier, il utilise une presse de coulée géante pour fabriquer un boîtier en aluminium monobloc. « Pas de soudures, pas de scellant, pas de joint multi-matériaux. Tesla utilise le gigacasting pour remplacer d’autres composants en acier estampé dans le corps en blanc, mais nous appliquons plutôt cette technologie aux batteries », a déclaré Harris.
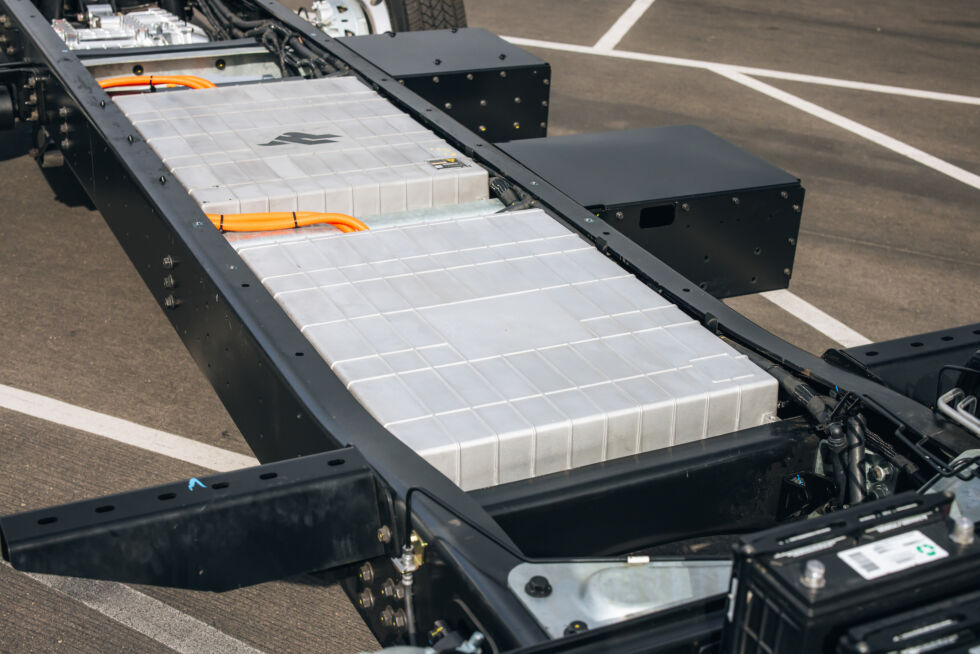
Présage
Comme Porsche et Hyundai, Harbinger a opté pour le 800 V pour ses batteries. L’avantage ici n’est pas vraiment pour une charge rapide plus rapide ; les flottes de camions de livraison qui parcourent rarement jusqu’à 160 km par jour se rechargeront lentement, mais surtout, à moindre coût, du jour au lendemain. (Cependant, la plate-forme a une capacité de charge rapide en une heure maximum.)
« C’est une masse positive, puis une efficacité par extension », a déclaré Harris. La tension plus élevée signifie un courant plus faible, qui à son tour signifie moins de poids ; Harris a déclaré qu’ils pouvaient utiliser un quart de la quantité de cuivre nécessaire à une architecture de 400 V. « L’autre élément qui fait une grande différence concerne les transmissions, car lorsque vous regardez le couple que vous pouvez obtenir d’un moteur électrique, dans de nombreux cas, il est proportionnel à la tension. Donc, si vous voulez un moteur de 400 volts, c’est bien plus grand. »
Harbinger construit également ses moteurs électriques en interne, intégrés dans une unité d’entraînement eAxle qui combine également une boîte de vitesses et un onduleur. Comme les batteries, il est suffisamment compact pour s’adapter entre les longerons du châssis, ce qui maintient le centre de gravité bas.

Présage
Parce que la conception est censée avoir une certaine longévité en service, Harbinger a été évolutif avec la direction et le freinage par câble afin qu’un système de conduite autonome puisse être intégré plus tard. Il aurait pu déjà s’associer à un développeur AV à cette fin, mais Harris pense que la décision du développeur AV à utiliser appartiendra aux opérateurs de flotte individuels comme UPS ou, plus précisément, à leurs services juridiques. « Et puis nous devons simplement soutenir cette décision. Et nous avons donc, nous pensons, la plate-forme parfaite pour eux. Pour ensuite installer leur logiciel, installer leurs capteurs, sans avoir à casser ce que nous avons déjà construit », a déclaré Harris.
Harbinger livrera des camions aux programmes pilotes des clients plus tard cette année pour commencer la validation. Et la conception et la fabrication en interne signifient que les camions Harbinger coûteront à peu près le même prix qu’un camion diesel ou essence de classe 4 équivalent. Tenez compte de la maintenance réduite et des coûts de charge beaucoup moins chers par rapport aux factures de carburant, et tout cela semble plutôt encourageant.